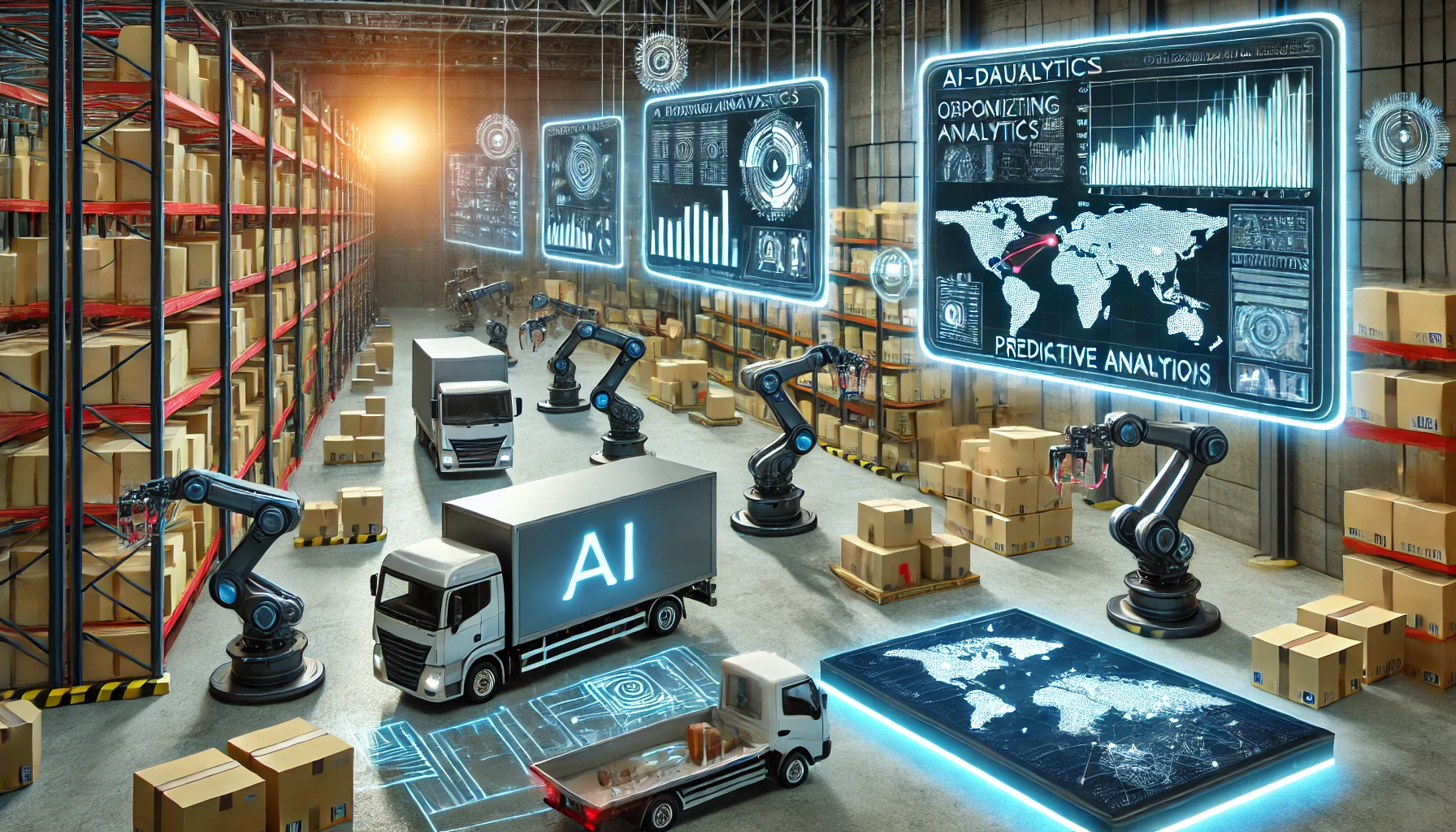
The Role of AI in Digital Transformation: A Guide for Supply Chain Businesses
AI is revolutionizing supply chains with smarter logistics, predictive analytics, and automation. Companies like Amazon and Walmart use AI for demand forecasting, route optimization, and inventory management, improving efficiency and reducing costs. Embracing AI ensures a competitive, future-ready supply chain.